June 18, 2019
Networking the right way
How does Connected Machining work in practice? Let’s produce a bicycle pedal using a HEIDENHAIN control as the central pivot of digital communication.
Digitalization. Networked production. Intelligent factories. These and several other buzz phrases are hot topics the currently discussed in manufacturing industries. We would like to explain how we view these topics and which solutions we offer with Connected Machining by way of an example—the production of a bicycle pedal.
What might a production infrastructure look like in which all work steps are digitally networked via Connected Machining, from construction to the ready-to-deliver component? At first glance not so different to traditional production in fact, because the participants are the same. Only the data flow between the individual stations is now digital and completely paper-free—in the case of Connected Machining with the HEIDENHAIN control on the shop floor as the central pivot of communication.
The networking protagonists usually consist of:
- Design including CAM programming and simulation
- Tool preparation and tool provision
- The workshop with machine tool and HEIDENHAIN control
- Quality inspection
- Procurement logistics for blanks and tools
- Supply logistics for the shipping of finished products
- Job planning and processing
At the center of the digital network: the HEIDENHAIN control
Using our example of digitally networked production let’s start where the actual added value is generated—on the shop floor. The secured blanks are lying on a pallet at the machine for pending work. But how do you, as the machine user, know what to do?
Usually you are given a folder or order pouch with all possible information on a few (or sometimes many) sheets of paper: drawings, parts lists, tool lists, deadlines, etc. And then you get going—trying to find something in the documents. They’re seldom sorted so you can gain a quick insight into the production-relevant data.
You won’t need this folder anymore in a digitally networked production environment with Connected Machining. Via the control, e.g. a TNC 640, you have direct access from the shop floor to all of the company’s relevant production data, which in turn is also networked.
Direct exchange: construction data and NC program
With HEIDENHAIN’s Remote Desktop Manager option you can directly access the CAM system from the HEIDENHAIN control. The CAM system on the other hand utilizes the information from the tool database for program creation.
Stay informed: job planning
Using the Batch Process Manager of the TNC 640 you can now schedule a production job’s execution right on the machine. NC programs and the position of the workpiece fixture on the pallet are linked according to the specific job. Batch Process Manager also provides you with information about the machining duration. It can also be used for order planning, such as scheduling further logistics of the finished parts or subsequent jobs for the machine.
On time and networked: tool reordering
The data from job planning is used together with tool management data to order new tools. The tool preparation station immediately receives orders for any additionally required tools. Based on the data stored in tool management, the tool preparation station can then promptly prepare new tools in the tool presetter for calibration.
In this case as well, the exact tool settings data is sent to tool management. The pre-set tools are given their own unique code on the tool holder for clear identification. Then the CAM program and virtual machine also have access to this data.
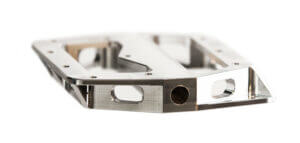
The finished workpiece: a bicycle pedal for downhill bikes
All information at hand: tool data and tools
Calibrated tools are already loaded in the machine’s tool magazine. They are clearly identified by a code on the tool holder. You have conveniently used a scanner to read this code while filling the tool magazine. The TNC 640 therefore knows immediately which tools are in the machine. The data comes directly from the tool management system via Ethernet.
For safety reasons the control automatically compares the tools used in the NC program with the tools actually available on the machine. The control then reports any tools that are missing, and states the estimated machining time. You can output a list of tool differences that contains only those tools you still need to prepare.
Consistently better processes: quality assurance
At the end, automatic calibration of the workpiece on the machine provides you with important data for quality assurance purposes. With the help of the control you can then simply archive the data or directly evaluate it. Naturally the data is also centrally available to all other systems, meaning that from the NC program to the tools, all links of the process chain can be optimized.