September 1, 2015
Leine & Linde PROFINET Gateway adds flexibility to motion system implementations
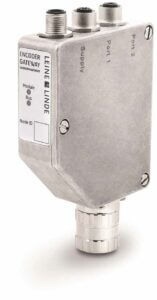
Leine & Linde PROFINET Gateway
CONTACT:
Bob Setbacken, Product Manager, 805-562-1160
Kathleen Stoneski, PR Manager, North America, 847-519-4702
Schaumburg, IL (September 2015)— Leine & Linde Gateway products allow the motion system designer to include virtually any encoder with an EnDat interface into their application. Now adding a PROFINET Gateway to the mix, Leine & Linde makes this addition simpler than ever, and will also support CanOPEN, DeviceNet, and PROFIBUS interfaces as well.
The benefit of the HEIDENHAIN EnDat encoder interface is that it allows a wide variety of robust absolute encoders suitable for high temperatures and harsh environmental conditions to be easily connected to industrial networks. Furthermore, the use of a Gateway allows for exchanging encoders without interrupting bus communication to other nodes in the network, thereby reducing downtime when disaster strikes.
The PROFINET Gateway is well-suited for the data exchange with bus cycle times of a few milliseconds, and allows any EnDat 2.1 or 2.2 encoder to connect to a PROFINET bus system.
The PROFINET Gateway supports encoder profile PNO 3.162 v.4.1 and is supplied with a GSDML configuration file and user manual providing detailed information for programming and application. The GSDML and user manual can be downloaded from the Leine & Linde webpage.
The gateways are available in two mechanical variants. Both variants have 3xM12 connectors for the PROFINET connection, but for the encoder input, either a M23 or M12 connector is available.
For more information, contact Bob Setbacken at HEIDENHAIN at 805-562-1160, or e-mail at bsetbacken@heidenhain.com, or write to HEIDENHAIN CORPORATION, 333 E. State Parkway, Schaumburg, IL 60173.
Leine & Linde is based in Sweden with exclusive North American distribution through HEIDENHAIN CORPORATION in Schaumburg, IL. Leine & Linde is well known for offering high quality, heavy duty encoders of both the incremental and absolute type, are noted for their product robustness and design to cope with the harshest of environments, such as those with high vibration, dirt and cold temperatures. These heavy, severe duty encoders are suited for drive and measurement applications and are often found in industries such as pulp and paper, forest and wood processing, agriculture, aggregate and mining equipment.