March 19, 2019
Interface diversity standardizes drives
Measurement technology for accuracy and connectivity
Moving machine applications require highly specific encoders capable of fulfilling widely varying requirements. Accuracy and reliability are not the only ones. For machine and equipment manufacturers, another crucial factor for any rotary, angle or linear encoder is its mechanical and electronic connectivity. Connectivity allows the manufacturer to standardize the design of his drive solutions and reduce the number of motor variants while not limiting the breadth of potential applications.
Interface diversity: always be well connected
HEIDENHAIN offers a wide range of encoders for accurate and highly accurate applications. This is because, regardless of the industry in which HEIDENHAIN products are used, simple connection options should always be available for every application. Included in this connectivity are mechanical and electronic connections, as well as connections between individual components and within complex networks. This diversity of interfaces in various combinations allows machine manufacturers to select the encoder best suited to their drive solutions.
Electronic connectivity: use data to increase equipment availability
When it comes to electronic connectivity, trouble-free communication with the machine or equipment controller is a crucial criterion in the selection of an encoder. But this goes beyond the reliable and correct transmission of position data. Of considerable importance is also the transfer of additional information, such as for commissioning, monitoring, and diagnostics. By contributing to the avoidance of machine downtime and reducing the number of maintenance cycles, these data can increase equipment availability and simplify process planning. Position encoders from HEIDENHAIN are available for this purpose, with a wide variety of interfaces:
- HEIDENHAIN EnDat
- Siemens DRIVE-CLiQ*
- Fanuc Serial Interface
- Mitsubishi High Speed Interface
- Panasonic Serial Interface
- Yaskawa Serial Interface
- SSI
- Profinet**
- 1 VPP
- TTL
- HTL
- And many more
Purely serial interfaces: reduce cabling and increase information
The trend is moving toward purely serial interfaces and the transmission of absolute position data. By eliminating the need for analog signals, this technology offers potential savings in the cabling required between the position encoder and the subsequent electronics. To this end, the position values are digitalized in the encoder and then sent to the subsequent electronics. This minimizes the negative influences on position information quality and data transmission that can arise when sinusoidal signals are used, and it increases the attainable position resolution compared with that of incremental interfaces using TTL or HTL output signals.
Encoder data and more: simplify commissioning and function monitoring
A digital interface for position data also enables the transmission of the “electronic ID label,” which contains data for the commissioning of the encoder and the drive. Digital interfaces also transmit additional information such as the temperature of the motor winding or diagnostics data—information that is dependent on the interface. For example, the EnDat 2.2 interface makes it possible to quickly and reliably provide information about the functional condition of the position encoder during operation, as part of regular maintenance, or in the event of a malfunction. Maintenance measures can then be derived from this information.
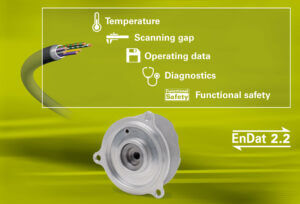
Mounting compatibility: flexibly choose accuracy
Thanks to the mechanical and electrical compatibility of many HEIDENHAIN encoders, a machine and equipment manufacturer can always select the optimal solution for his specific control requirements from the HEIDENHAIN product program. He can thus keep the number of motor variants to a minimum without limiting the breadth of potential applications.
HEIDENHAIN solutions include different shaft diameters and mounting flange variants for rotary and angle encoders, scale tape solutions for extremely large radii or long measuring distances, and encoders with mechanically safe connections. Mounting compatibility is also available for many encoders with different measuring principles. For example, most HEIDENHAIN encoder versions with incremental and absolute measured-value acquisition are available with mounting compatibility. These absolute rotary encoders are further subdivided into singleturn and multiturn variants with gears or battery buffer for the counting of complete revolutions.
One motor, two possible system accuracies
HEIDENHAIN’s ECI/EQI 1100 and ECI/EQI 1300 inductive rotary encoders feature mounting compatibility with the ECN/EQN 1100 and ECN/EQN 1300 rotary encoders with optical scanning and integral bearing. In practice, this means that switching from an inductive rotary encoder to a mechanically compatible optical rotary encoder can improve the system accuracy of a given motor from ±65” to ±20”.
Match the graduation carrier to the application
HEIDENHAIN linear encoders from the LIDA series are available with various graduation carriers (steel, glass, or glass ceramic) and a corresponding variety of measuring accuracies. Depending on the variant, these encoders measure the position at accuracy grades ranging from ±15 µm (steel) to ±1 µm (glass ceramic). The various mounting options of the individual designs ensure versatile usage in highly diverse applications.
Exclude errors with functional safety
Functional safety is playing an increasingly important role in the field of machine tool manufacturing. For encoders, this means that position data must always be correctly and precisely ascertained and transmitted to the machine control. Other important aspects of functional safety include encoder diagnostics and mechanical fault exclusion. Encoders from HEIDENHAIN feature user-friendly solutions for a wide range of safety-related applications.
The safety levels
- In conjunction with a safe control, HEIDENHAIN encoders satisfy all of the requirements for safety-related applications in conformity with SIL 2 (as per EN 61508) or Performance Level “d” (as per EN ISO 13849).
- When properly implemented in the subsequent electronics, some encoders are also suitable for systems in conformity with SIL 3 (as per EN 61508) or Performance Level “e” (as per EN ISO 13849).
Mechanical fault exclusion: extra support for the control
Examples of encoders for a safe connection to the drive are the functional safety versions of the ECN/EQN 400 series. These encoders feature a hollow shaft connection featuring mechanical fault exclusion for the blind hollow shaft in diameters of 10 mm or 12 mm. As a result, faults that are undetectable by the control, such as the slippage of a friction connection, can be avoided.
Safety, system monitoring, and function reserve: three’s the charm
Thanks to serial interfaces, HEIDENHAIN encoders also provide complete information for commissioning, monitoring and diagnostics. This information supports the analysis of complex machines, thereby making an important contribution to the topic of Industry 4.0. HEIDENHAIN makes diagnostics much easier through the use of valuation numbers, which enable the assessment of an encoder’s function reserve. The high level of expertise formerly required for the evaluation of encoder signals is no longer necessary. This design feature is also available with other interfaces besides EnDat.
Encoder diagnostics: how HEIDENHAIN is unique
HEIDENHAIN is the only encoder manufacturer to offer a diagnostic tool for all of its encoders with absolute and incremental interfaces: the adjusting and testing package consisting of the PWM 21 and the ATS software. With this package, the condition of the encoder can be tested during machine operation (online diagnostics during active operation of the axis) and as part of mounting or repair work (offline diagnostics).
Evaluate the function reserve with ease
For the evaluation of the function reserve in closed-loop operation, HEIDENHAIN encoders generate valuation numbers. These easy-to-understand numbers provide detailed information about the state of the following factors:
- The internal scanning signal
- Position-value formation
- The encoder itself
Based on these data, controls or inverters can provide statements about the function reserve. The scale and meaning of these numbers are identical for all HEIDENHAIN encoders, allowing for evaluation across the board. Transmission is performed in a closed control loop, and the resource usage in the subsequent electronics is relatively low, since only numerical values are evaluated and displayed.