October 8, 2009
HEIDENHAIN rotary encoders in elevator technology
Updated on [10/18/2021]
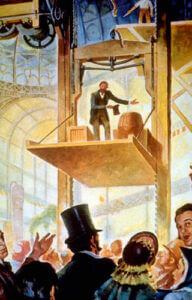
Figure 1 – Mr. Otis demonstrates the safety brake
The development of elevators began as early as the mid-1800’s. At a trade show in New York, a man shocked a crowd of spectators as he stood on an elevator platform at maximum height (Fig. 1) and cut the platform’s only bearer cable.
The platform sank by only a few centimeters before it immediately stopped. This pragmatic mechanic’s revolutionary new safety brake ensured that the platform didn’t crash. “All safe, gentlemen!” he announced. The man on the elevator platform was Elisha Graves Otis. Otis sold his first safety elevator in 1853.
Elevator efficiency gains can be attained to increase the load capacity while reducing required installation space, reduce noise while increasing traversing speeds, lengthen maintenance intervals, and reduce environmental pollution in spite of increased performance.
The drive technology employed is an essential factor in achieving these goals. While years ago the high-volume segment still operated on drive designs with frequency-controlled gear motors and hydraulic installations (motors with pumps), the technology transformed itself in the late 1990s to direct drives (permanent-magnet actuated synchronous motors with high pole-pair numbers), also known as torque motors.
Thanks to the freedom from maintenance and the power density of torque motors, it was also possible to integrate them in the elevator shaft and do without the machine room. This option was as welcome to architects as it was to building owners because it enabled them to realize new building designs and savings.
The technology of these motors frequently requires an absolute position value to ascertain the rotor position so that the motor current is controlled with the correct phase. Also, the relatively low rated speed (60 to 1500 rpm) of these drive designs made high-resolution position acquisition a must to be adequate to the short control cycle times.
Rotary encoders for elevators
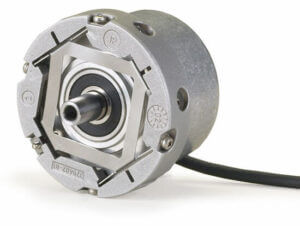
Rotary encoders of the ECN/ERN 1300 Series
Here the story begins to become interesting for HEIDENHAIN with its broad offering of rotary encoder products. Because of these requirements, the rotary encoders of the ExN 13xx series, which were developed for the high-quality drive control needed in machine tools and printing machines, also find application in today’s changing elevator drive technology. To be able to withstand the environmental conditions of an elevator shaft (e.g., concrete dust), some of the encoders have to be modified for a higher protection grade (sealing the housing and using sealed ball bearings). This came together with a market requirement for providing large cable lengths from the encoder (up to 10 m) without using extensions.
So, with relatively few R&D expenses, the rotary encoders for servo motors became the ERN 487 and ECN 413, encoders optimized for use in elevator motors. In addition, the simple, purely axial installation of the encoders permits streamlined integration in the motor design with mounted brake. Besides the encoders of the ExN 13xx/4xx series, which have established themselves in the low to medium motor power range, manufacturers also use the ExN 1xx series encoders for application in high-rise buildings.
Through further evolution over the years, encoders can be used for the feedback control of various motor designs in the elevator industry, such as internal, external, or disc motors.
Most important characteristics for motor control in elevators
- Rigid shaft connections
- High mechanical natural frequencies for rotary encoder couplings
- Wide runout tolerances
- Easy mounting
- For absolute encoders, a high-performance bidirectional interface, like EnDat
Rotary encoders for elevators with diagnostics and feedback
In the near future, microswitches will no longer be needed for brake release monitoring. That’s because encoders like the KCI 419 Dplus rotary encoder provides not only position feedback, but also additional data for monitoring.
Currently, elevator brakes are monitored by means of separate microswitches. In addition to transmitting rotational position values, this kind of inductive rotary encoder also measures the amount of axial travel. When mechanically coupled with the armature plate of the brake, it can detect the brake stroke.
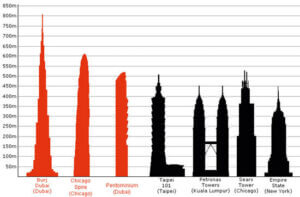
(Red: not yet completed)
An encoder like the KCI 419 Dplus considerably enhances availability and safety thanks to temperature monitoring and comprehensive online self-diagnostic capabilities. By virtue of its direct proximity to the motor and brake, the encoder can provide meaningful temperature monitoring data without additional sensors or cabling. The temperature data can then be used to pinpoint wear, plan maintenance, and predict the occurrence of malfunctions.
Rotary encoders for elevator shaft copying
Shaft copying is used to ensure jerk-free braking and precise positioning of the elevator car. These systems measure the car’s position and forward it to the control. Incremental rotary encoders and especially absolute rotary encoders are ideal for this application. These encoders enable digital shaft copying with clear benefits for control technology and installation.
The key advantage of using absolute multiturn rotary encoders for position detection is the continuous availability of the car’s absolute position (even after a power failure). Since actual position values are available at all times, the car can approach its destination rapidly. A bearing assembly with an EQN 400 is offered specifically for shaft copying. Elevator car position is often measured by means of toothed belts and deflection pulleys. Thanks to the bearing assembly, the resulting forces are decoupled from the precision bearing of the rotary encoder, preventing encoder overload.
Rotary encoders for elevator door motors
In high-rise buildings with large elevator capacities and high passenger traffic, shorter stopping times are an important goal, allowing more passengers to be transported. A critical factor in handling a building’s passenger traffic is proper elevator door operation. Fast and precise opening and closing with minimal noise requires servo-controlled door motors. Compact rotary encoders are particularly well suited for speed and position feedback.
The future of elevators is gearless, cableless and horizontal
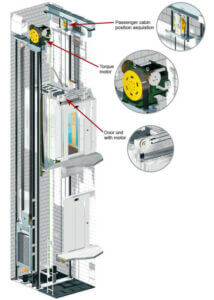
Modern elevator design with the three possible applications for encoders:
– Passenger cabin position acquisition
– Torque motor
– Door unit with motor
Modern cable-bound elevators have two significant restrictions resulting from their design: Due to the weight of the cable itself, it is almost impossible to further increase the travel heights, and as a rule, only one cab can travel up and down an elevator shaft. This strongly limits the number of passengers that can be transported.
The demands on elevator technology in recent years have called for higher speeds, higher shafts, smaller footprints, and lower operating costs. To answer these calls, elevator manufacturers are considering ways to build cable-less elevators. This technical idea borrows from the Transrapid, the high-speed magnetic levitation train developed in Germany. Similarly, the elevators of the future will be powered with the aid of direct linear-motor technology.
The cab is equipped with passive magnets, and the active stator, divided into segments, is located in the elevator shaft. By appropriately providing current to these individual segments, multiple cabs can travel inside a shaft—independently of each other.
Permanent-magnet synchronous motors are often used due to their higher power density. Depending on the control strategy, these motors may require absolute position feedback for proper rotor position control. Most of these demanding drive systems also require high-resolution rotary encoders integrated into the control loop as position encoders for measurement of the actual speed.
Benefits of gearless elevator motor systems with proper feedback
- Low vibration and noise
- Reduced space requirements thanks to machine-room-less elevators (MRL)
- Comfortable ride characteristics
- Low energy consumption
- Low maintenance and oil-free
Linear encoders for horizontal transportation
In addition to the vertical motion, the gearless, cableless concept permits horizontal motion. This horizontal motion makes it possible to use new technology for the increasingly long level distances in tall mega buildings and in sprawling but connected building complexes.
The main challenge presented to the motor control during the linear motion is the tolerance required for guideway deviations, since the control must simultaneously provide high signal quality for controlling the direct drive. Only excellent measuring signals reduce vibrations, permit dynamic motions, and significantly increase the speed stability, while at the same time avoiding the generation of additional heat.
Linear encoders like the LINA 200 have been designed specifically for cable-less elevators. Initial tests showed that traveling speeds of 6 m/s are achieved easily, and in the laboratory the LINA 200 provided reliable position values at speeds of up to 18 m/s. At slow speeds, as well as during acceleration after a stop and braking before a stop, the high resolution of the position values (18 bits) at a measuring length of approximately 600 mm ensures a very comfortable and gentle motion.
The elevator industry has been on a consistent trajectory toward frictionless mechanics and digital diagnostics. The encoder and feedback technology is already available and will play a huge role in this transition in buildings across the globe.