December 3, 2018
Constantly reliable position acquisition
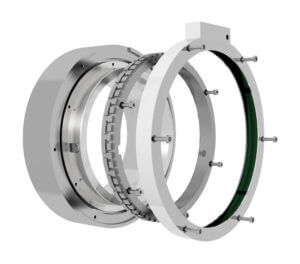
The scale drum (center) of the ECI 4000 is securely connected to the motor mechanics (left) thanks to a keyway (on the right: the scanning unit)
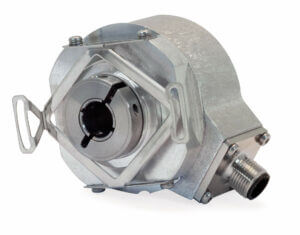
ECN 400 and EQN 400 with functionally safe mounting
Functional safety is playing an increasingly important role in machine-tool manufacture. For encoders, that doesn’t only mean correctly and accurately measuring position data and transferring it to the machine control. Functional safety also includes encoder diagnostics and mechanical fault exclusion. Encoders from HEIDENHAIN satisfy OEMs with user-friendly solutions for the most diverse safety-related applications.
Machines and plants are getting faster and more flexible, but also more sophisticated and expensive. This applies for machine tools as much as for pick-and-place machines in automation or die-cast systems for plastic processing. In view of the high investment costs for such high-tech machines, owners expect high availability and predictability of their plants and processes. At the same time, legal safety regulations for the operation of the systems are increasing. The result of this development is the growing significance of functional safety.
HEIDENHAIN offers a comprehensive program of rotary encoders, angle encoders, and linear encoders for safety-related applications. They provide all necessary prerequisites to achieve classification for safety-related applications in accordance with SIL 2 (as per EN 61 508) or performance level “d” (as per EN ISO 13849) in conjunction with a safe control system. They also meet high requirements regarding dynamics and accuracy, which, thanks to their serial interfaces, also provide all the information necessary for commissioning, monitoring and diagnostics. In all variants, the universally applicable phase meter PWM 20 together with the evaluation software ATS supports the user on site during diagnosis and installation.
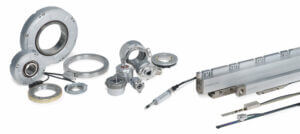
Angle and linear encoders from HEIDENHAIN for safety-related applications.
Safe mechanical connection
An example for the safe connection of the measuring device to the drive are the rotary encoders of the ECN 400 and EQN 400 series in functional safety version. They offer a functionally safe hollow shaft connection with mechanical fault exclusion for their blind hollow shafts with diameters of 10 mm or 12 mm. This mechanical fault exclusion avoids faults that cannot be detected by the controller, such slippage of a frictional connection. The other end of the diameter range with shaft diameters up to 512 mm is served by the functional safety versions of the ECA 4000 absolute modular angle encoders.
With these two examples and numerous other solutions for safety-related applications such as the ERM magnetic angle encoders or the LC 415 or LC 495 absolute sealed encoders, HEIDENHAIN covers a wide range of applications in machines and systems. Magnetic angle encoders and inductive rotary encoders are particularly suitable for use in production machines that expose their components to high mechanical loads.
HEIDENHAIN encoders for safety-related applications with optical and magnetic scanning | ||||
---|---|---|---|---|
ECN 400 EQN 400 | ECA 4000 | LC 415 LC 495 S | ERM 2200 | |
Fault exclusion for mechanical coupling | √ | √ | √ | √ |
Version for safety-related applications | √ | √ | √ | – |
HEIDENHAIN encoders for safety-related applications with inductive scanning | ||||
---|---|---|---|---|
ECI 1119 EQI 1131 | ECI 1319 EQI 1331 | ECI 4010 | AMO WMI AMO WMIA | |
Fault exclusion for mechanical coupling | √ | √ | √ | √ |
Version for safety-related applications | √ | √ | √ | — |
Vibration 55 Hz to 2000 Hz (EN 60 068-2-6) | Stator: ≤ 400 m/s2 Rotor: ≤ 600 m/s2 | Scanning unit: ≤ 400 m/s2 Scale drum: ≤ 600 m/s2 | ≤ 200 m/s2 |
Uniform diagnostic data
Through its EnDat interface, a HEIDENHAIN encoder generally transmits the following information relevant for plant availability:
- The error message has to lead to a safe system condition. At the same time, this means that it causes a system shutdown.
- A warning indicates that an internal function limit has been reached. It serves as an early warning system for preventive and projectable maintenance without triggering immediate machine downtime.
- Diagnostic data provide detailed information on the position encoder’s functional reserve.
For encoders with a purely serial EnDat 2.2 interface, a comprehensive diagnosis is conducted in the encoder, whereby warnings and error messages are generated. Error messages are transmitted with high priority with each position value transmission to the subsequent electronics. To evaluate the function reserve in closed closed-loop operation, HEIDENHAIN encoders generate so-called evaluation numbers. The easy-to-understand valuation numbers provide detailed information about the state of the internal incremental and absolute scanning signals as well as the position value formation and thus on the current condition of the encoder. Controls or inverters can use these data to make conclusions about the functional reserve. Their scale and significance is identical for all HEIDENHAIN encoders, so that a universal assessment is possible. They are transmitted in the closed control loop and do not burden the time for position transmission. The load on the subsequent electronics’ resources is relatively small, because it need only display numerical values. The availability of the valuation numbers and access to them depend on the respective customer-specific interface.
Simple commissioning
A digital interface for position data also enables the transmission of the so-called electronic ID label, i.e. data for commissioning the encoder and the controller. It also transmits additional data such as the winding temperature of the drive or diagnostic data. The transmitted data are dependent on the interface. For example, the EnDat 2.2 interface allows information about the functional state of the position encoder to be transmitted quickly and reliably during operation, regular maintenance or in the event of a fault. Such factors represent important basis data for condition monitoring or for making statements concerning the capacity and planning of systems and processes.
Interfaces and diagnostic data supported by HEIDENHAIN encoders | |||||||
---|---|---|---|---|---|---|---|
Range of functions and diagnostics of the PWM 20 and ATS software for serial interface | EnDat | Fanuc | Mitsubishi | SSI | DRIVE-CLiQ* | Yaskawa | Panasonic |
Display of online diagnostics | √ | √ | √ | — | √ | √ | √ |
Display of online diagnostics in the control loop | √ | √ | √ | — | — | — | √ |
Feed-through mode permitted with PWM 20 | √ | √ | √ | — | — | — | √ |
Circular representation of the incremental signals (if available) | √ | — | — | √ | — | — | — |
Display of supply voltage and current | √ | √ | √ | √ | √ | √ | √ |
*DRIVE-CLiQ is a registered trademark of SIEMENS AG |
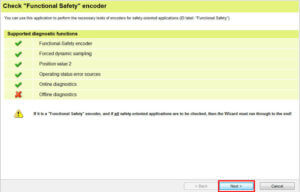
… or for the supported diagnostic functions of an encoder in its functional safety version.
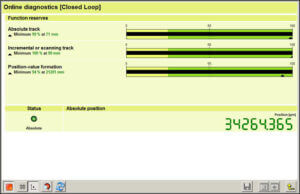
Straightforward and informative: the display of the ATS software, here for example the functional reserve of an encoder …
Various testing and inspection devices are available for the diagnosis and adjustment of HEIDENHAIN position encoders. The inspection device with the broadest application range is the PWM 20. Together with the ATS software, it makes possible the analysis of almost all HEIDENHAIN position encoders with the interfaces listed in the table above. During installation of modular encoders, the PWM 20 uses ATS software to check whether the measuring standard and the scanning unit match each other. If the encoder is connected directly to the PWM 20, a detailed analysis of the encoder functions is possible. If the PWM 20 is looped into the closed loop—if necessary by means of suitable test adapters—a real-time diagnosis of the machine or system is possible during operation. The safety functions can also be triggered and checked via the PWM 20 during initial commissioning or when exchanging encoders for safety-related applications.
The unique combination of high-accuracy position measurement, a large number of available interfaces and simple diagnostics make HEIDENHAIN position encoders an important performance and quality factor for highly dynamic and highly accurate machines and systems.