September 12, 2019
Bearing the load of complex motion control
Developing new products often forces manufacturers of highly accurate machines to push the envelope of the technologically possible. At this juncture, HEIDENHAIN provides support for robust systems with new motion control solutions perfectly tailored to the requirements of many different applications and industries.
The more demanding the application, the simpler the solution can be. This seeming paradox can actually be true when the right partners work together, merging their strengths and expertise from different fields. The resulting solutions can take different forms. This fact is evident from the new system solutions for position measurement from HEIDENHAIN, which range from modular (and thus flexibly deployable) devices such as the HEIDENHAIN ERP 1000, to the highly integrated HEIDENHAIN angle encoder modules.
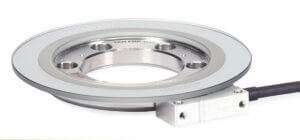
The new ERP 1000 modular angle encoders: accurate and robust measured data acquisition combined with flexible integration options.
The new ERP 1000 modular angle encoder: redefining high-end applications
During development of the new ERP 1000 modular angle encoders, HEIDENHAIN focused not only on accurate and robust measured point acquisition but also gave special priority to enable flexible integration into the customer’s complete system. This goal was achieved by offering a wide selection of variants in different circular scale sizes. The circular scales are available as full-circle and segment versions in diameters of 57 mm, 75 mm, 109 mm, and 151 mm, and can thus accommodate virtually any customer-specific requirement. Compact dimensions and very low mass enter into the equation as well. The scanning head is a mere 26 mm long, 12.7 mm high, and 6.8 mm wide, and features a mass of only 5 g. Depending on the version, the circular scales are at most 10.2 mm high, with the lightest full-circle scale weighing in at only 57 g.
HEIDENHAIN made the ERP 1000 modular angle encoders to be easy for users to mount. As non-paired systems, all of the versions feature generous mounting tolerances and convenient automatic signal adjustment. A wide selection of cable and connector versions is available for the electrical connection. As a result, flexible adaptation and integration into the customer-specific system is a straightforward affair.
Thanks to its special characteristics, the ERP 1000 family is redefining angle measurement capability in high-end applications—not only in terms of flexibility but also in terms of accuracy and robustness. With the ERP 1000, these benefits are achieved through the encoder’s optical scanning principle and the first-ever deployment of the HEIDENHAIN HSP 1.0 signal processing ASIC within an angle encoder. These modular angle encoders thereby achieve accuracy grades down to ±0.9 arc seconds while maintaining excellent signal quality. Their interpolation error can be as low as ±0.02 arc seconds, and their RMS position noise can be as little as 0.002 arc seconds. These values apply even in highly dynamic applications with speeds of up to 2600 rpm. Consequently, the ERP 1000 modular angle encoders are particularly well suited to applications requiring exceptionally constant speed control or high position stability at standstill.
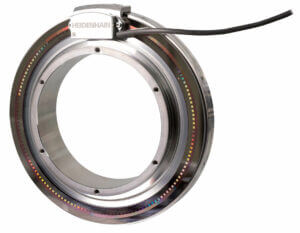
Highly integrated system: the MRP angle encoder modules feature tested and specified characteristics (MRP 8000 shown). The machine manufacturer no longer needs to develop its own bearing.
The MRP angle encoder module: eliminate the need for your own bearing
The machine manufacturer receives the HEIDENHAIN MRP angle encoder modules in the form of completed assemblies with specified characteristics. These assemblies combine high-resolution measurement technology with a dependable high-precision bearing. For the machine manufacturer, this system solution provides two special benefits: it eliminates the need for the costly and separate development of a rolling or air bearing, and the HEIDENHAIN bearing is capable of handling off-center tilting loads. Manufacturers of metrology systems, in particular, stand to benefit significantly in the designing of highly accurate rotary axes.
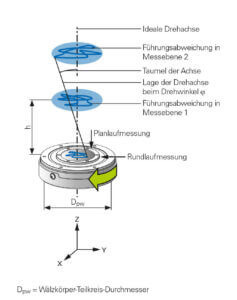
Crucial for the accuracy of the angle encoder module: measured values and measuring locations on the precision bearing.
The angle encoder modules are characterized by their high degree of measuring and bearing accuracy, very high resolution, and extremely high repeatability. Also noteworthy is their low starting torque, which provides for smooth motion. Instead of numerous individual components, a highly integrated assembly with tested and specified characteristics is now available due to the fact that HEIDENHAIN has already completed the assembly and adjustment of all components. The characteristics of the angle encoder modules have therefore already been defined and tested in conformity with the specifications desired by the customer. Thanks to the system’s simple mechanical interfaces, critical mounting processes are eliminated. The painstaking adjustment of the components relative to each other and the machine environment is thereby rendered superfluous, including the effort that normally goes toward testing.
Because HEIDENHAIN manufactures both the bearing and the encoder, these two functional assemblies are harmoniously integrated. Compared with a conventional solution, fewer components are necessary, and thus fewer joints as well. This permits an extremely rigid and compact design featuring a particularly low overall height. Angle encoder modules are currently available with hollow shaft diameters of 10 mm, 35 mm, and 100 mm.
The integrated rolling bearings have been adapted specifically to the requirements of high-precision rotary axes. Key benefits include the system’s very high guideway accuracies, high rigidities, low starting torques, and smooth continuous torque. HEIDENHAIN has developed a special procedure for assessing the bearing accuracy by evaluating the actual guideway accuracy of the bearing (i.e., the deviation between the actual rotary axis and the nominal rotary axis). Both the radial and axial guideway accuracies, as well as the amount of wobble, are all specified. As in the past, a distinction continues to be made between reproducible and nonreproducible errors.
In view of these factors, the MRP angle encoder module can serve as a realistic alternative to axes with air bearings. Although the absolute guideway accuracy of an air bearing is doubtless better than that of a rolling bearing in many cases, the repeatability of the angle encoder modules from HEIDENHAIN is comparable to the guideway accuracy of an air bearing. The rigidity of the HEIDENHAIN rolling bearing is also greater by a factor of at least 10 compared with that of air bearings of similar size. As a result, the HEIDENHAIN rolling bearings may actually be the more accurate solution on axes subjected to loads. Rolling bearings also feature the advantages of being generally less sensitive to shock loads and of not requiring a controlled air supply, making them robust and easier to handle.
Angle encoder module with integrated drive: the next level of system integration
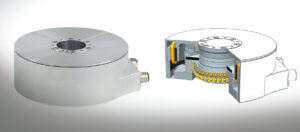
HEIDENHAIN angle encoder modules with an integrated torque motor from ETEL: high-accuracy motion, guidance, and measurement, all within a single compact system.
The integration of a torque motor with very low cogging torque is the next logical step beyond the MRP angle encoder module design. This combination enables extraordinarily smooth motion control for high-accuracy positioning and measurement tasks. Neither disruptive cogging torque nor radial forces influence the high guideway accuracy of the bearing. This marriage of an angle encoder module with motor components yields a particularly compact system featuring a low profile and high rigidity. And it is precisely this rigidity of the components that ensures accuracy even under varying loads.
A so-called slotless torque motor from ETEL serves as the drive motor. This motor combines the seemingly contradictory properties of high torque density and low cogging torque. The reason for this lies in the motor’s special, symmetrical design featuring a self-holding coil. The slots associated with conventional windings are thereby eliminated. As a result, this motor has no cogging torque, and, in combination with the angle encoder module, enables extraordinarily smooth motion.
Thanks to the clever arrangement of the main components, noise has very little effect on control and measurement accuracy. The design also permits very compact dimensions and a sizeable hollow shaft. AccurET controllers from ETEL are the perfect match for the angle encoder modules with drive motor, providing top dynamic and position stability performance.
In particular, the new angle encoder modules with integrated motor are optimized for the demanding requirements of metrology applications. Very high resolution and excellent repeatability at varying operating temperatures are key, while high motor torques are generally not very important in this context. For the perfect adaption to individual requirements, customer-specific modifications are possible as well.