Powerful functions for 5-axis machining
Five-axis machining expands your range of machinable parts and boosts productivity. Other benefits include less rechucking, shorter production times, and fewer sources of error. For complex parts, 5-axis machining is an essential element in your production process.
The TNC 640 from HEIDENHAIN supports the user with numerous practical functions that make 5-axis machining easy and reliable, from programming to part inspection.
Master the challenge of 5-axis machining
with HEIDENHAIN
5-axis machining: reliable mastery with the TNC 640
5-axis machining: powerful TNC functions for aerospace parts
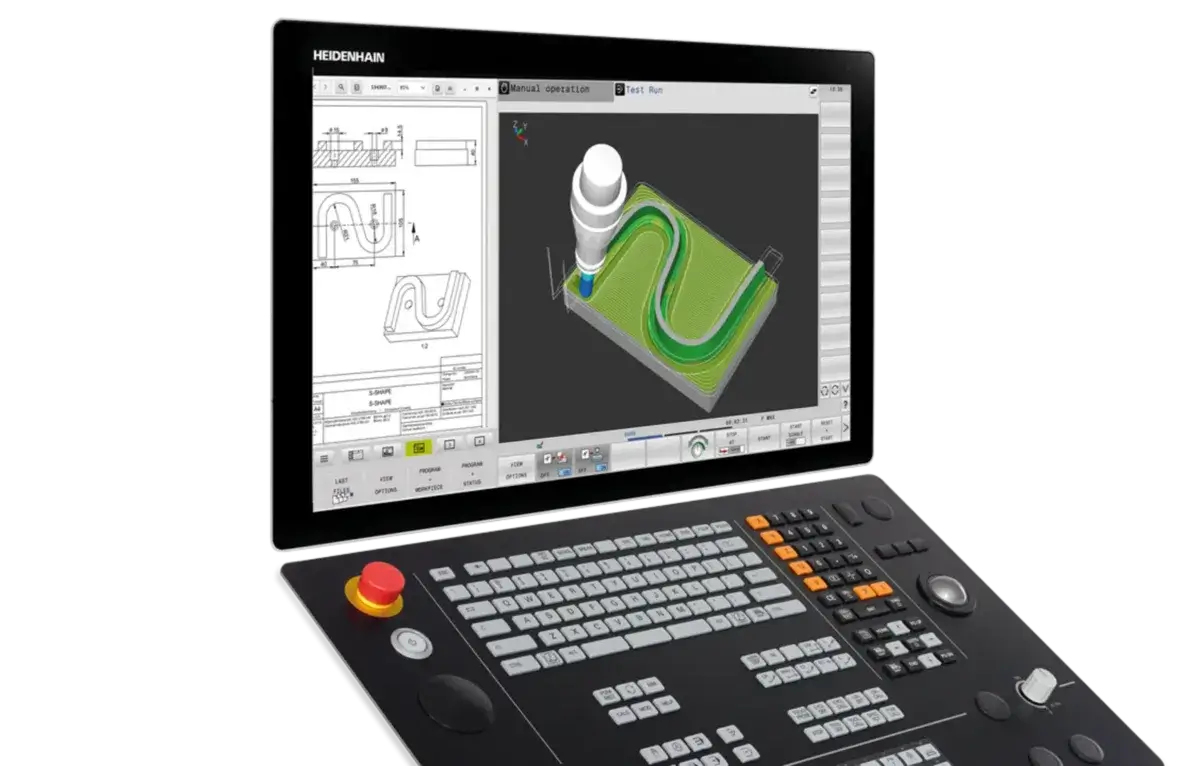
Your benefits with the TNC 640 for
5-axis machining
- Prevention of machine damage and downtime
- Precise machine kinematics model in the control
- Reliable roughing processes under consistent cutting conditions
- Cross-system 5-axis machining
- Perfect surfaces in very short machining times
- Improved accuracy at the tool center point
- Easy and efficient part inspection
Prevent machine damage and downtime
Realistic simulations let you reliably verify the NC program before machining. With a programming station, you can do this from the convenience of an office while leveraging the high realism of our Digital Twin. During setup and production, Dynamic Collision Monitoring prevents collisions during complex 5-axis motion.
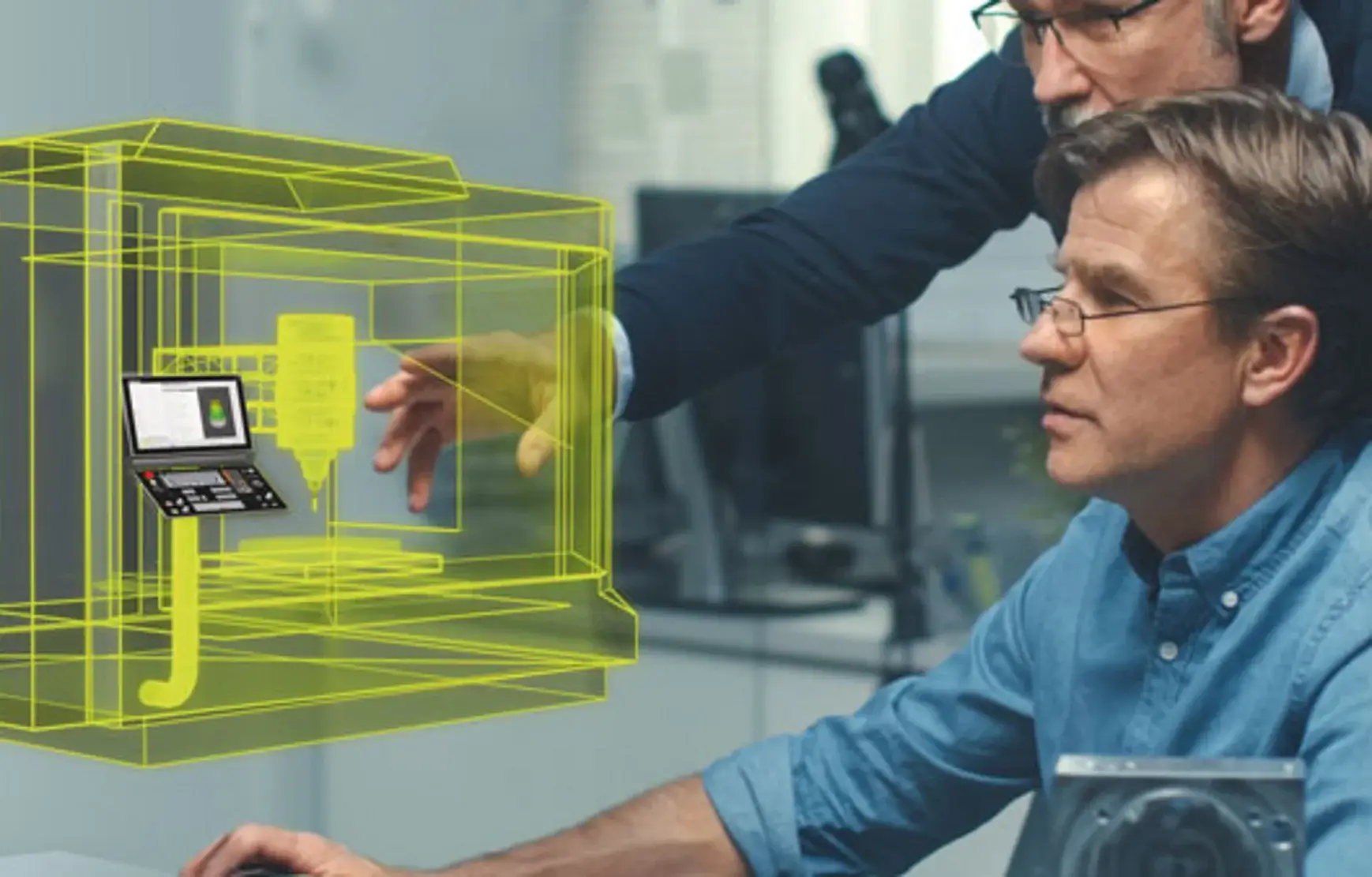
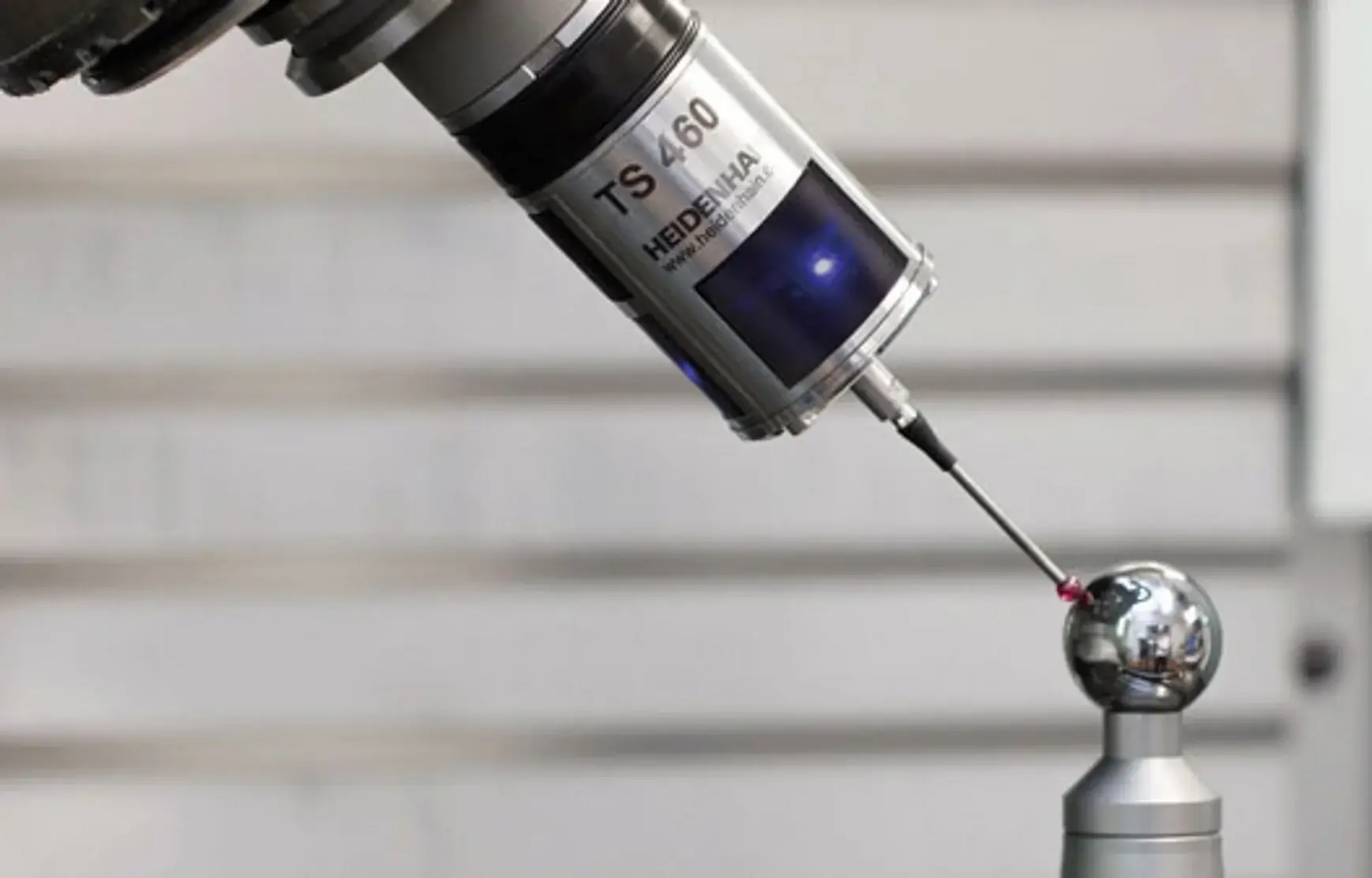
Precise machine kinematics model in the control
Shop-friendly calibration cycles ensure consistent machine accuracy. The KinematicsOpt function lets you inspect the accuracy of rotary and swivel axes as well as compensate for any shift in the center of rotation. Any error is automatically accounted for in the kinematics description.
Reliable roughing and finishing processes under consistent cutting conditions
High-efficiency roughing and finishing cycles for tool-friendly machining are essential for productive 5-axis machining. With Optimized Contour Milling (OCM), the control automatically calculates the complex motion needed in trochoidal milling for creating pockets and islands of any shape. The integrated cutting data calculator makes it easy to calculate the optimal cutting values.
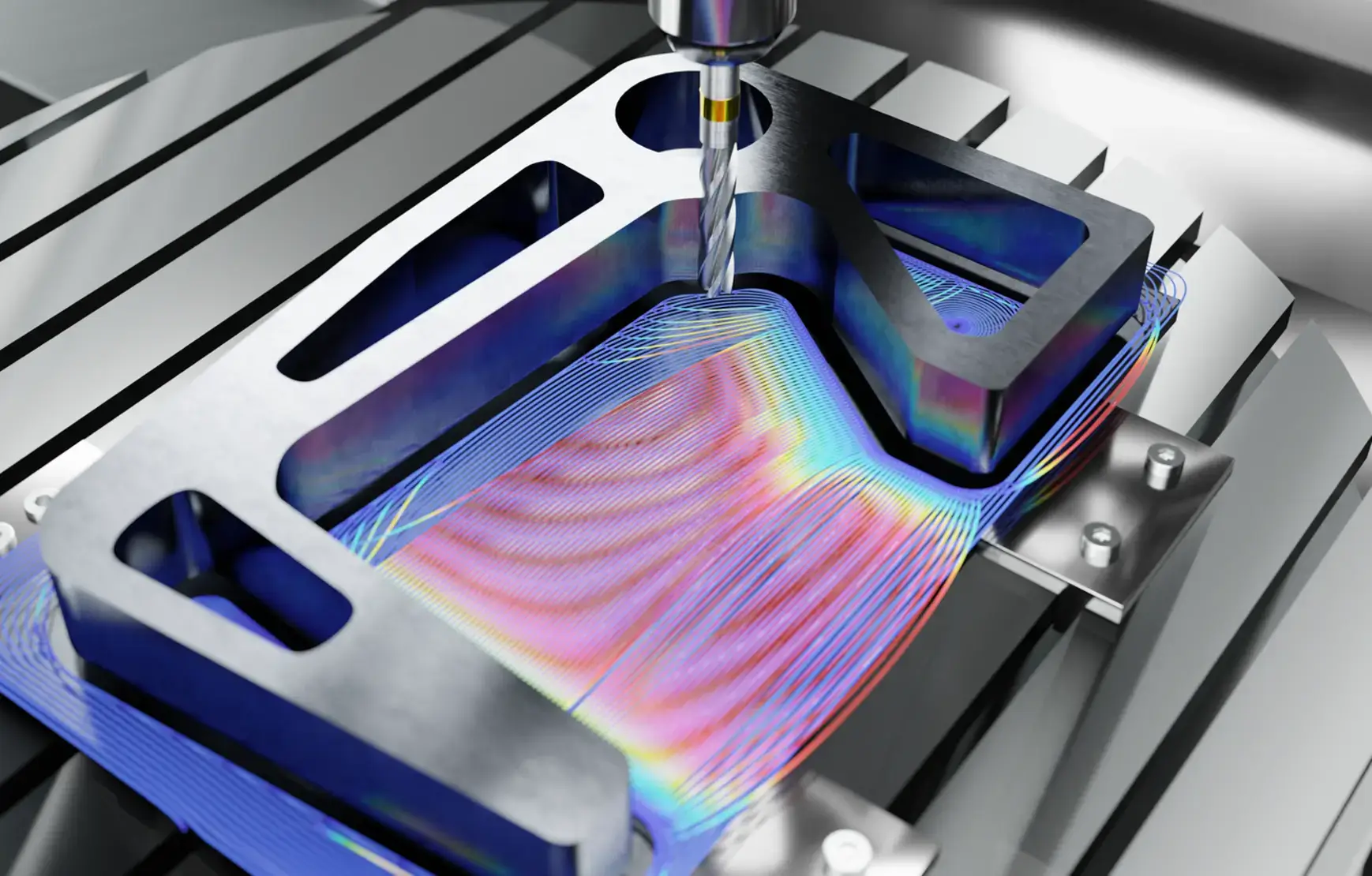
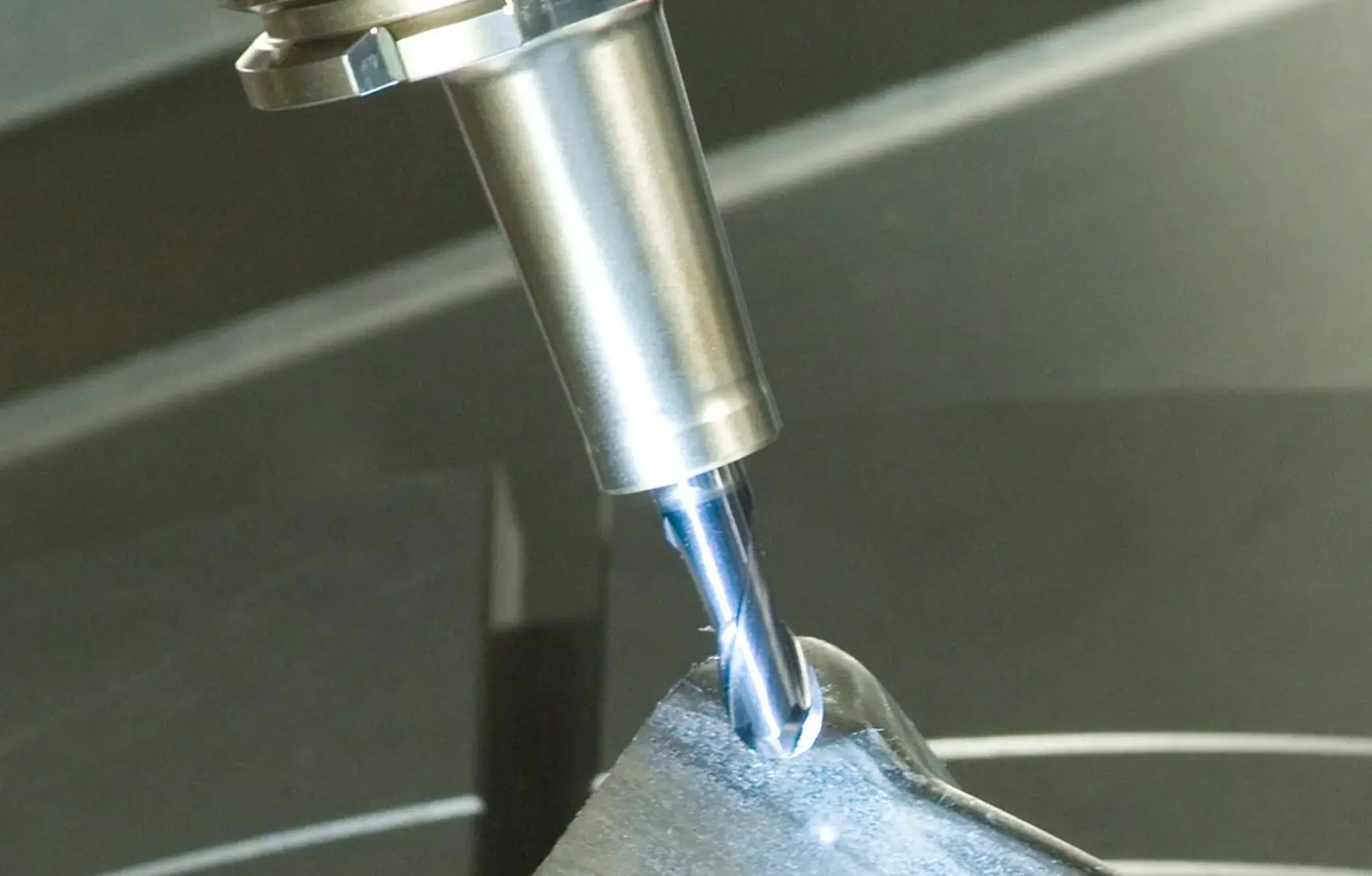
Cross-system 5-axis machining
The TCPM function enables optimal tool guidance. 3D-ToolComp compensates for tool radius errors. As a result, 5-axis machining with the TNC 640 creates a perfect part in very little time, putting you in the lead whenever optimal machining results and efficient processes are called for.
Perfect surfaces in very short machining times
In addition to optimal tool guidance, motion guidance plays a key role in machining results and performance. Cycle 32 TOLERANCE adapts the machine contour tolerances to the specific machining operation for the perfect combination of accuracy and dynamic performance.
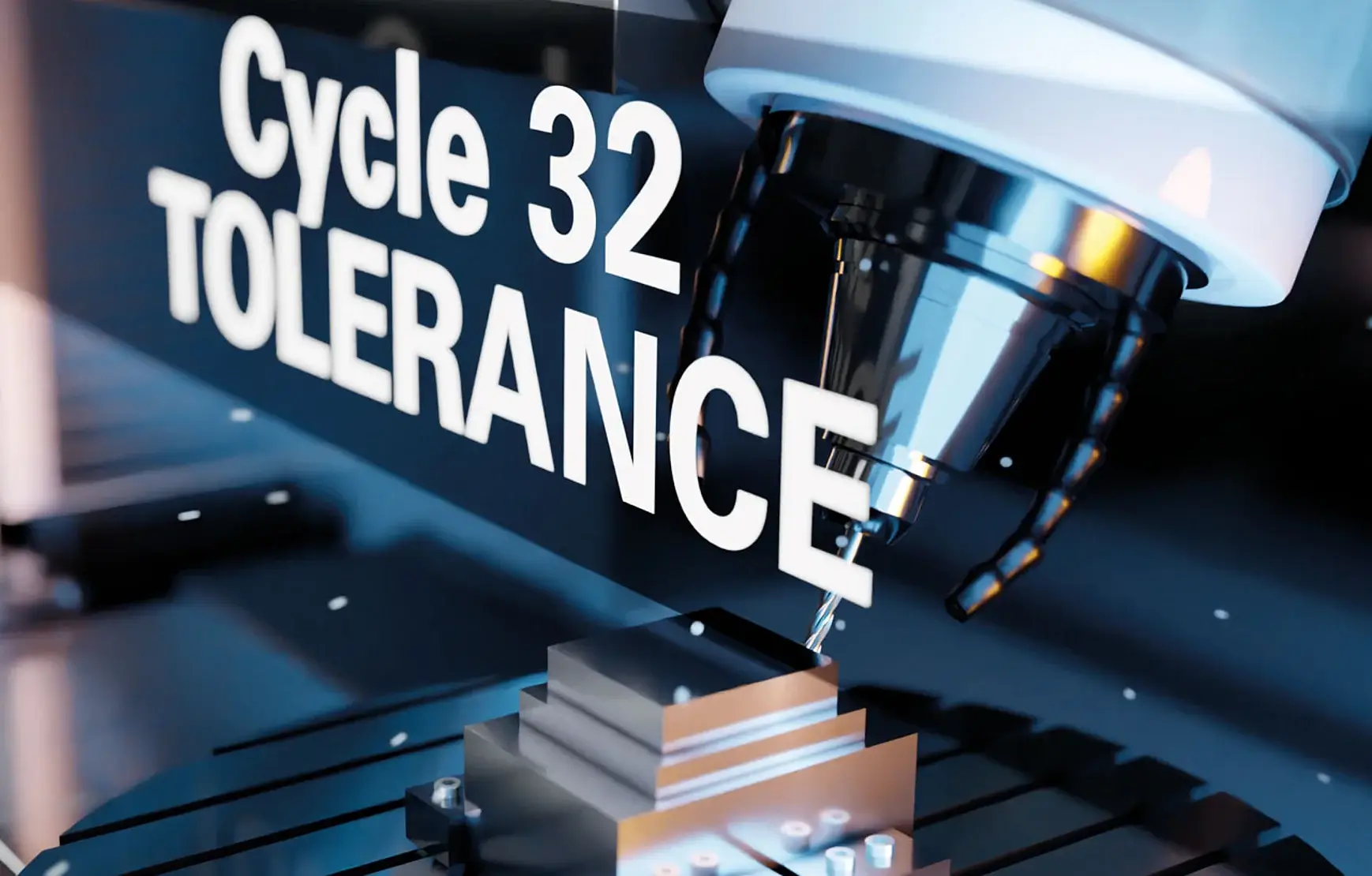
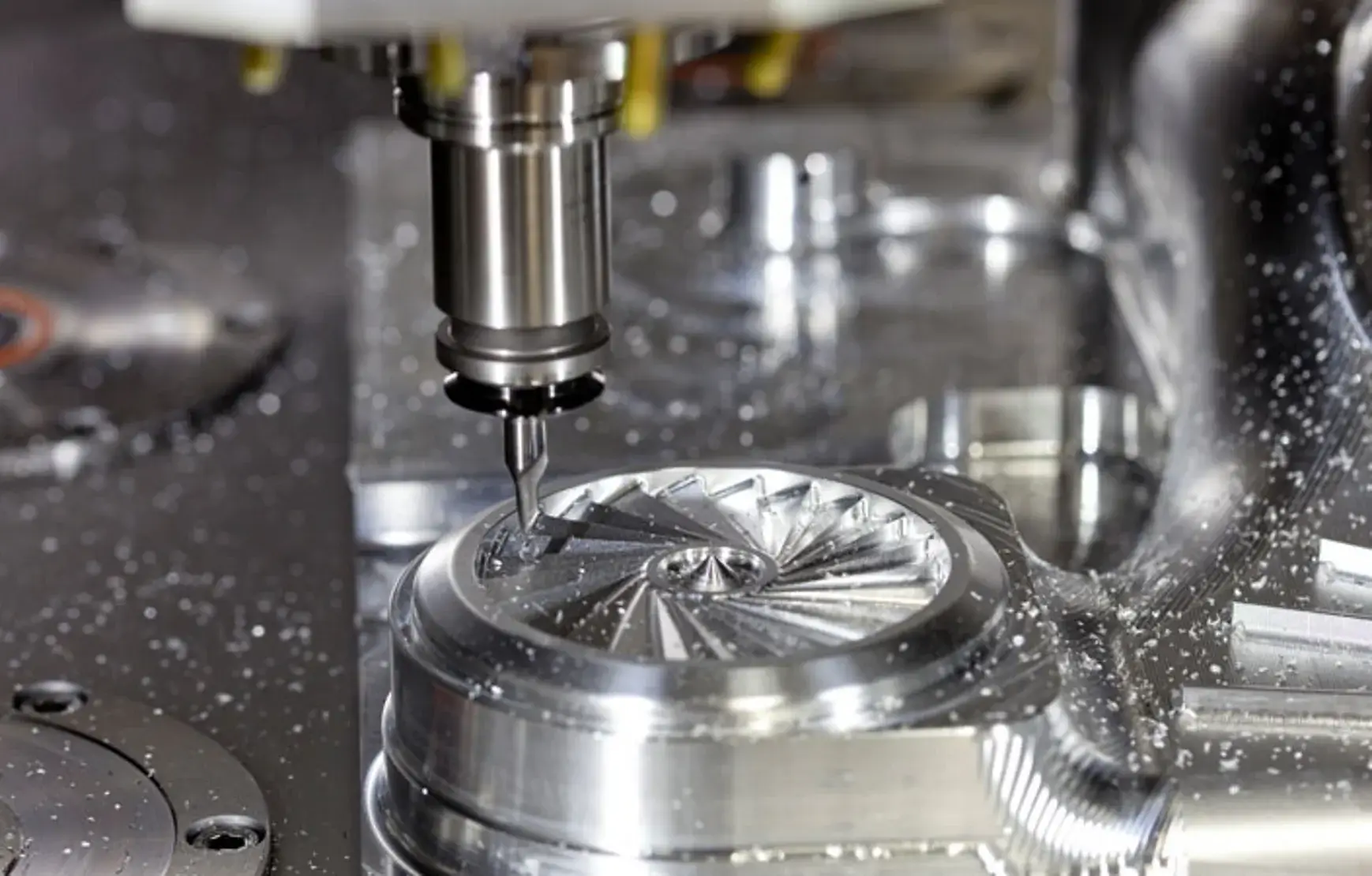
Improved accuracy at the tool center point
The functions of Dynamic Precision systematically compensate for dynamic errors, thereby teasing out the full potential accuracy of a machine tool. Rapidly machined parts with higher contour accuracy and superior surfaces are the result.