We build the indispensable subcomponents
Robotic machinery and automation technology rely on countless smaller parts and pieces working seamlessly to deliver new levels of efficiency and throughput. In this world, components aren’t just commodities. Don’t trust unmanned motion to just anyone.
How can we help?
What is a dual encoder for robots?
What is EnDat and how can a feedback interface possibly be described as the “future of manufacturing”?
How do manufacturers begin implementing automation?
Where do you see industrial automation trends heading in the next few years?
What’s the surprisingly crucial role motion control plays in the cloud computing mega trend?
Solutions tailored for process automation robotics
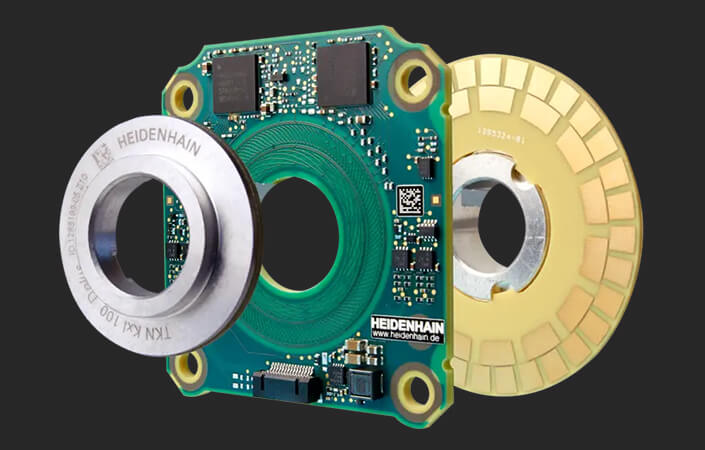
Motor feedback and position measurement all in one
The KCI 120 Dplus dual encoder provides motor feedback and position measurement in a single device. Installed downstream from the gear system, it enables the compensation of design-related inaccuracies in dynamic robots, such as joint elasticity, zero-position error, reversal error, and machining effects. The encoder’s purely serial EnDat 2.2 interface with functional safety permits deployment in applications such as human-robot collaboration.
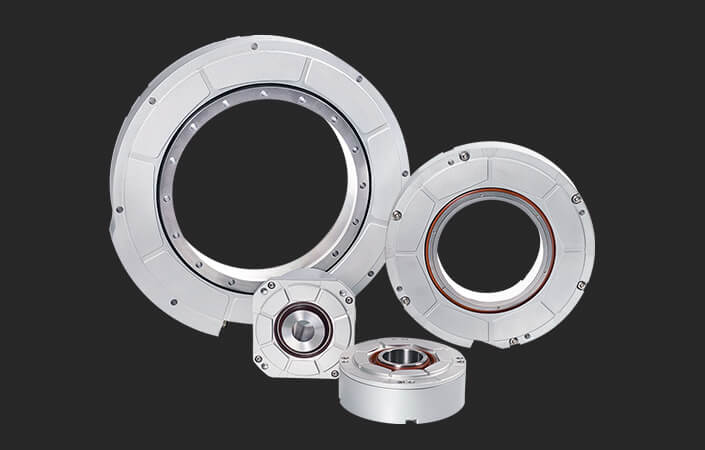
Secondary encoders for additional accuracy
The absolute position accuracy of your robots can also be improved by adding a high-accuracy angle encoder to each axis. Mounted downstream from the gear system, secondary encoders measure the actual position of each robot joint. We offer modular encoder solutions for this purpose, such as the HEIDENHAIN ECA 4000 with optical scanning, the AMO WMRA angle encoder system, and angle encoders from RSF. These encoders are well suited to large shaft diameters and challenging installation requirements, making them ideal as secondary encoders.
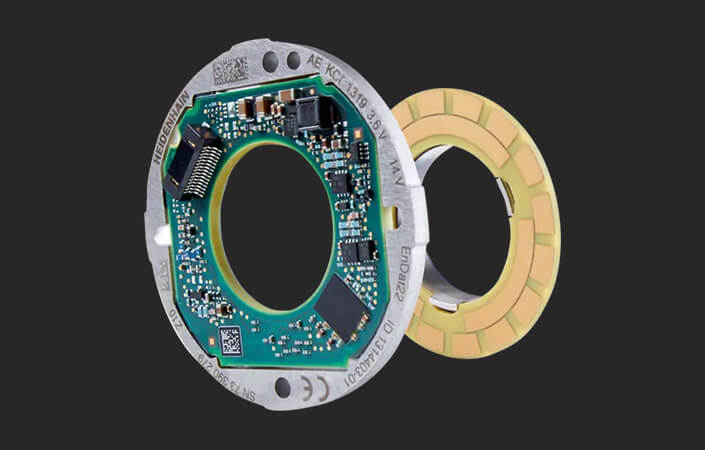
Low-weight, low-profile encoders for robot motors
The KCI 1300 and KBI 1300 rotary encoders deliver inductive scanning capability in a low-weight, low-profile design, making them ideal for compact servomotors in robots. Their reliable inductive scanning method makes them insensitive to contamination and magnetic fields. The diagnostic data they provide enable condition monitoring, including motor monitoring via an external temperature sensor. Consisting of just a scanning unit and a screw-fastened circular scale or a disk/hub assembly press-fit to the motor shaft, the KCI 1300 and KBI 1300 are easy to install thanks to their wide mounting tolerances.